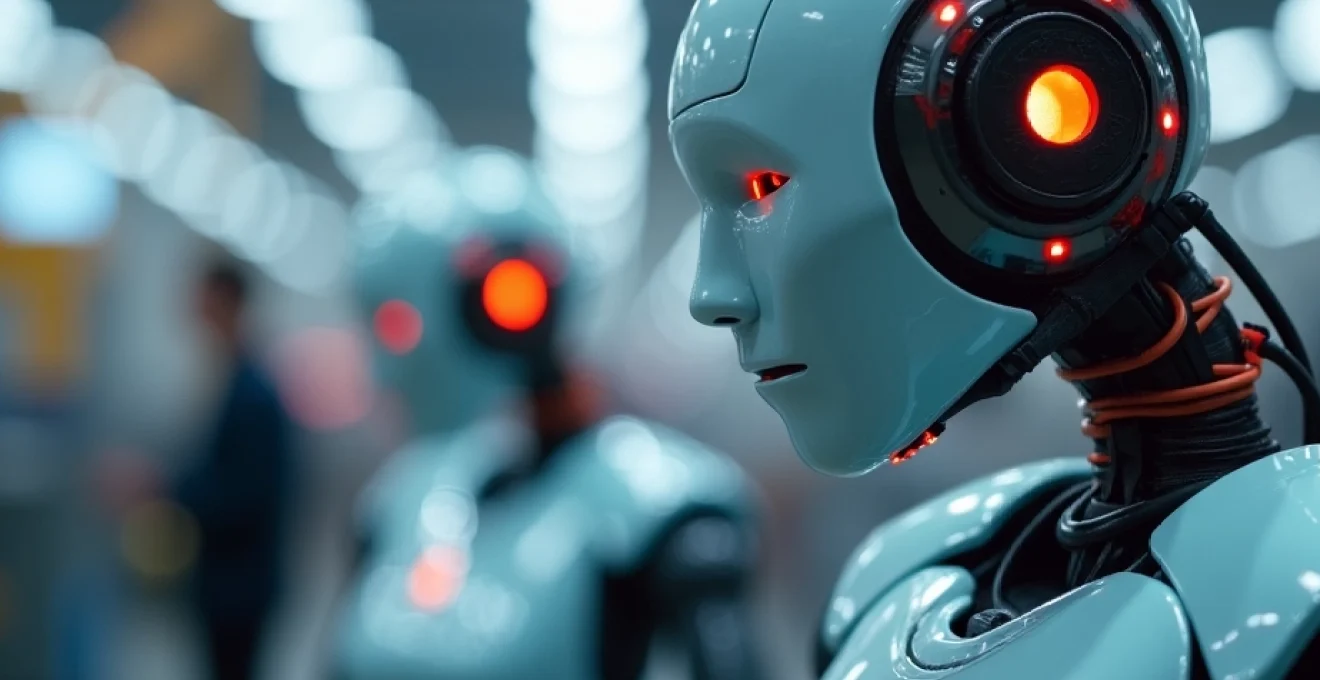
The manufacturing landscape is undergoing a revolutionary transformation, and at the forefront of this change are collaborative robots, or cobots. These advanced machines are reshaping production lines, enhancing efficiency, and redefining human-robot interaction in ways previously thought impossible. As industries strive for greater productivity and flexibility, cobots are emerging as a game-changing solution that combines the precision of automation with the adaptability of human workers.
Collaborative robots represent a paradigm shift in industrial automation. Unlike their traditional counterparts, cobots are designed to work alongside human operators, sharing workspaces and tasks in a safe, efficient manner. This symbiotic relationship between humans and robots is not just improving manufacturing processes; it's fundamentally altering the way we approach production challenges in the 21st century.
Evolution of collaborative robots in manufacturing ecosystems
The journey of collaborative robots from concept to reality has been nothing short of remarkable. Initially introduced as a solution to enhance workplace safety and flexibility, cobots have rapidly evolved to become integral components of modern manufacturing ecosystems. Their development has been driven by a need for more agile production methods capable of adapting to increasingly dynamic market demands.
In the early stages, cobots were primarily used for simple, repetitive tasks. However, as technology advanced, so did their capabilities. Today's cobots are sophisticated machines capable of performing complex operations with high precision. They can be easily programmed and reprogrammed to handle a variety of tasks, making them ideal for manufacturers who need to quickly adapt their production lines to meet changing consumer preferences.
The integration of cobots into manufacturing has led to the creation of hybrid workforces, where human ingenuity and robotic efficiency complement each other. This synergy has resulted in significant improvements in productivity, quality, and workplace ergonomics. As a result, manufacturers are experiencing reduced operational costs and increased output, all while maintaining a focus on worker well-being.
Key technologies enabling cobot integration
The successful integration of collaborative robots into manufacturing environments is made possible by several key technologies. These innovations have not only enhanced the functionality of cobots but have also ensured their safe and effective collaboration with human workers. Let's explore some of the most critical technological advancements driving the cobot revolution.
Advanced sensors and machine vision systems
At the heart of cobot functionality are advanced sensors and machine vision systems. These technologies enable cobots to perceive their environment with remarkable accuracy, allowing them to navigate complex workspaces and interact safely with humans and objects. High-resolution cameras and 3D sensors provide cobots with real-time data about their surroundings, enabling them to make split-second decisions and adjustments.
Machine vision systems go beyond simple object detection. They can identify specific parts, assess quality, and even read barcodes or QR codes. This level of visual acuity allows cobots to perform intricate tasks such as precision assembly or detailed inspection processes with minimal human intervention.
Force-torque feedback mechanisms
Force-torque sensors are crucial components that give cobots a sense of touch. These sophisticated feedback mechanisms allow robots to apply just the right amount of force when handling objects or interacting with surfaces. This capability is particularly valuable in tasks that require delicate handling or precise manipulation of materials.
By continuously monitoring the forces applied during operation, cobots can adjust their movements in real-time. This not only ensures the safety of human co-workers but also prevents damage to products or equipment. The ability to "feel" their way through tasks makes cobots incredibly versatile and suitable for a wide range of manufacturing applications.
Intuitive programming interfaces and teach pendants
One of the most significant barriers to robot adoption in the past has been the complexity of programming. Modern cobots address this issue with intuitive programming interfaces and user-friendly teach pendants. These tools allow operators to program cobots through simple demonstrations or graphical interfaces, drastically reducing the learning curve and setup time.
Teach pendants, which are handheld devices used to control and program robots, have evolved to feature touchscreens and intuitive interfaces. This allows even workers with limited programming experience to quickly set up and modify cobot tasks. As a result, manufacturers can rapidly reconfigure their production lines to meet changing demands without relying on specialized programmers.
Ai-driven task learning and adaptation
Artificial intelligence is revolutionizing the capabilities of collaborative robots. AI-driven systems enable cobots to learn from experience and adapt to new situations autonomously. Through machine learning algorithms, cobots can optimize their performance over time, improving efficiency and reducing errors.
This adaptive learning capability is particularly valuable in dynamic manufacturing environments where product specifications or production processes may change frequently. Cobots equipped with AI can quickly adjust to new tasks or variations in their work environment, minimizing downtime and maximizing productivity.
Safety standards and protocols for Human-Robot collaboration
As collaborative robots become more prevalent in manufacturing settings, ensuring the safety of human workers remains paramount. The development and implementation of robust safety standards and protocols have been crucial in enabling the widespread adoption of cobots. These guidelines provide a framework for manufacturers to integrate cobots into their operations while minimizing risks to human workers.
ISO/TS 15066 compliance in cobot design
The International Organization for Standardization (ISO) has developed specific technical specifications for collaborative robot systems. ISO/TS 15066 provides guidelines for the design and implementation of collaborative robot systems, focusing on safety requirements and risk reduction strategies. Compliance with these standards ensures that cobots are designed with inherent safety features that allow them to work alongside humans without the need for protective barriers.
Key aspects of ISO/TS 15066 include specifications for speed and separation monitoring, power and force limiting , and hand guiding operations. By adhering to these standards, cobot manufacturers can create machines that automatically slow down or stop when a human enters their workspace, significantly reducing the risk of accidents.
Risk assessment methodologies for collaborative workspaces
Implementing cobots in a manufacturing environment requires a thorough risk assessment to identify potential hazards and develop appropriate mitigation strategies. This process involves evaluating the specific tasks the cobot will perform, the layout of the workspace, and the interaction points between robots and humans.
Risk assessment methodologies for collaborative workspaces often include:
- Identifying potential hazards associated with cobot operations
- Evaluating the likelihood and severity of potential incidents
- Implementing control measures to reduce risks to acceptable levels
- Regularly reviewing and updating safety protocols as processes evolve
Power and force limiting technologies
One of the key safety features of collaborative robots is their ability to limit the power and force exerted during operation. This is achieved through advanced sensors and control systems that continuously monitor the robot's movements and interactions with its environment. If a cobot detects unexpected contact or resistance, it can instantly reduce its force or come to a complete stop to prevent injury.
Power and force limiting technologies allow cobots to operate without protective barriers, making them ideal for tasks that require frequent human interaction. This capability not only enhances safety but also improves efficiency by enabling seamless collaboration between robots and human workers.
Safety-rated monitored stop functions
Safety-rated monitored stop functions are another critical component of cobot safety systems. These functions allow cobots to quickly and reliably come to a stop when a human enters their workspace or when an abnormal situation is detected. The stop function is monitored by redundant safety systems to ensure that the robot remains in a safe state until it is manually restarted by an operator.
This feature is particularly important in applications where humans need to frequently enter the robot's workspace to load or unload parts, perform quality checks, or make adjustments. By implementing safety-rated monitored stops, manufacturers can create flexible workspaces that promote collaboration while maintaining the highest levels of safety.
Industrial applications revolutionized by cobots
Collaborative robots are making significant inroads across various industrial sectors, transforming traditional manufacturing processes and opening up new possibilities for automation. Their versatility and ease of use have led to widespread adoption in diverse applications, from intricate assembly tasks to heavy-duty material handling. Let's explore some of the key industrial applications where cobots are making a substantial impact.
Precision assembly in electronics manufacturing
In the fast-paced world of electronics manufacturing, precision and consistency are paramount. Collaborative robots excel in these areas, making them ideal for intricate assembly tasks. Cobots equipped with advanced vision systems and force-sensing capabilities can handle delicate components with the utmost care, reducing errors and improving product quality.
For instance, in smartphone assembly lines, cobots are employed to place microchips, solder circuit boards, and even apply adhesives with micron-level accuracy. Their ability to work tirelessly without fatigue ensures consistent quality throughout long production runs, a critical factor in an industry where tolerances are measured in microns.
Flexible material handling in automotive production
The automotive industry has been quick to embrace collaborative robots for their flexibility and efficiency in material handling tasks. Cobots can be easily programmed to adapt to different car models or components, making them invaluable in modern, multi-model production lines.
In automotive plants, cobots are often seen working alongside human operators, assisting with tasks such as:
- Lifting and positioning heavy components like dashboards or seats
- Applying sealants or adhesives with precise pressure and consistency
- Performing repetitive tasks like screw-driving or clip insertion
- Assisting with final quality checks and inspections
Quality inspection and testing processes
Quality control is a critical aspect of manufacturing, and cobots are proving to be valuable allies in this domain. Equipped with high-resolution cameras and sensors, collaborative robots can perform detailed inspections with a level of consistency and accuracy that surpasses human capabilities.
In industries ranging from pharmaceuticals to aerospace, cobots are being deployed for tasks such as:
- Visual inspection of products for defects or inconsistencies
- Dimensional checks using laser scanning or touch probes
- Non-destructive testing procedures like ultrasonic or X-ray inspections
- Automated documentation and reporting of quality metrics
Machine tending and CNC integration
Machine tending is another area where collaborative robots are making significant strides. By integrating cobots with CNC machines, manufacturers can achieve higher levels of automation and efficiency in their machining processes. Cobots can load and unload parts, change tools, and even perform simple machining tasks, allowing human operators to focus on more complex aspects of production.
The benefits of using cobots for machine tending include:
- Increased machine utilization and productivity
- Reduced risk of operator injury from repetitive motions
- Improved consistency in part handling and positioning
- Enhanced flexibility to handle multiple part types or machine configurations
Economic impact and ROI analysis of cobot implementation
The adoption of collaborative robots in manufacturing is not just a technological advancement; it's a strategic business decision with significant economic implications. To understand the full impact of cobot implementation, it's essential to conduct a comprehensive return on investment (ROI) analysis. This evaluation helps manufacturers quantify the benefits and justify the initial investment in cobot technology.
When assessing the economic impact of cobots, several key factors come into play:
- Initial investment costs (hardware, software, integration)
- Operational cost savings (labor, energy, maintenance)
- Productivity improvements and increased output
- Quality enhancements and reduced waste
- Flexibility and scalability of production
One of the most significant advantages of cobots is their relatively low initial investment compared to traditional industrial robots. This lower barrier to entry makes them particularly attractive to small and medium-sized enterprises (SMEs) looking to automate their processes without breaking the bank.
Moreover, the flexibility of cobots allows for quick redeployment across different tasks or production lines, maximizing their utility and accelerating ROI. Many manufacturers report ROI periods of less than 12 months for their cobot investments, a remarkably short timeframe in the world of industrial automation.
The economic benefits of cobot implementation extend beyond direct cost savings. By enhancing productivity and quality, cobots can help manufacturers increase their market competitiveness and open up new business opportunities.
It's important to note that the full economic impact of cobots is not always immediately apparent. Intangible benefits such as improved worker satisfaction, reduced physical strain, and enhanced workplace safety contribute to long-term economic gains through reduced turnover and workers' compensation costs.
Future trends: cobots in industry 4.0 and smart factories
As we look to the future of manufacturing, collaborative robots are poised to play an even more significant role in the advent of Industry 4.0 and the development of smart factories. The integration of cobots with other advanced technologies is opening up new possibilities for automation and data-driven manufacturing processes.
Iot integration and Data-Driven cobot performance
The Internet of Things (IoT) is revolutionizing the way machines communicate and share data. In the context of collaborative robotics, IoT integration enables cobots to become part of a larger, interconnected ecosystem of smart devices and systems. This connectivity allows for real-time monitoring of cobot performance, predictive maintenance, and data-driven optimization of manufacturing processes.
By leveraging IoT technologies, manufacturers can:
- Monitor cobot performance metrics in real-time
- Predict maintenance needs before failures occur
- Optimize cobot movements and task sequences based on data analytics
- Integrate cobot operations with other smart factory systems for seamless production flow
Cloud-based collaborative robot management
Cloud computing is enabling new paradigms in robot management and control. Cloud-based platforms allow manufacturers to remotely monitor, program, and manage their cobot fleets across multiple locations. This centralized approach to robot management offers several advantages:
- Simplified software updates and deployment of new features
- Centralized storage and analysis of operational data
- Enhanced collaboration and knowledge sharing across manufacturing sites
- Scalable computing resources for complex AI and machine learning applications
Advancements in Human-Robot interaction (HRI) interfaces
As cobots become more prevalent in manufacturing environments, the importance of intuitive and efficient human-robot interaction interfaces grows. Future trends in HRI are focused on making the collaboration between humans and robots even more seamless and natural.
Emerging technologies in this area include:
- Advanced gesture and voice recognition for cobot control
- Augmented reality (AR) interfaces for programming and task visualization
- Haptic feedback systems for more precise manual guidance of cobots
- AI-powered natural language processing for complex task instructions
Scalable and modular cobot ecosystems
The future of collaborative robotics lies in creating scalable and modular ecosystems that can easily adapt to changing production needs. This trend is driven by the demand for more flexible manufacturing systems that can quickly respond to market changes and consumer preferences.
Key aspects of scalable cobot ecosystems include:
- Plug-and-play cobot modules that can be easily added or reconfigured
- Standardized interfaces for quick integration with existing machinery
- Flexible software platforms that support rapid task reprogramming
- Collaborative robot swarms that work together on complex tasks
As collaborative robots continue to evolve and integrate with other Industry 4.0 technologies, their impact on manufacturing will only grow. The future factory will likely see humans and cobots working side by side in increasingly sophisticated and efficient ways, driving innovation and productivity to new heights.
The transformation
of modern manufacturing through collaborative robots is well underway, promising a future where human ingenuity and robotic precision work in harmony to create more efficient, flexible, and innovative production systems. As cobots continue to evolve and become more integrated with other advanced technologies, they will undoubtedly play a crucial role in shaping the factories of tomorrow, driving productivity and competitiveness in the global manufacturing landscape.