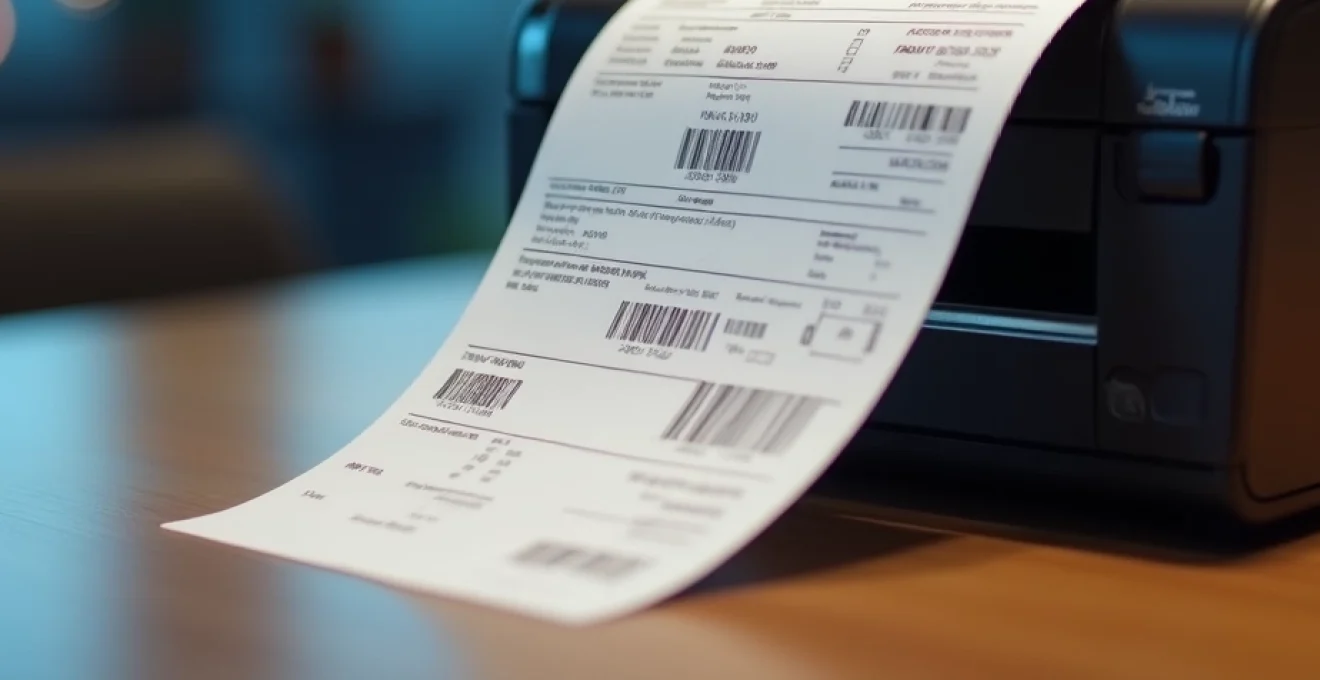
In the ever-evolving world of printing technology, thermal printing stands out as a robust and efficient solution for businesses across various industries. This innovative printing method offers unparalleled speed, reliability, and cost-effectiveness, making it an attractive option for organizations seeking to streamline their operations. As we delve into the intricacies of thermal printing, we'll explore its core mechanisms, compare different techniques, and examine its wide-ranging applications in today's fast-paced business environment.
Thermal printing technology: core mechanisms and principles
At its heart, thermal printing technology relies on the application of heat to create images on specially treated paper or labels. This process eliminates the need for traditional ink or toner, resulting in a simpler, more maintenance-free printing solution. The thermal printer uses a thermal printhead containing thousands of tiny heating elements that selectively activate to produce the desired image or text.
The precision and speed of this heat application process allow for high-quality prints with sharp resolution, making thermal printing ideal for barcode labels, receipts, and other critical business documents. Moreover, the absence of liquid ink means there's no risk of smudging or bleeding, ensuring consistently clear and legible output.
Direct thermal vs. thermal transfer: comparative analysis
When it comes to thermal printing, two primary methods dominate the landscape: direct thermal and thermal transfer. Each technique has its unique characteristics and applications, catering to different business needs and environmental conditions.
Direct thermal printing
Direct thermal printing utilizes heat-sensitive paper that changes color when exposed to heat from the printhead. This method is particularly popular for short-term use items such as receipts, shipping labels, and event tickets. The simplicity of direct thermal printing lies in its lack of additional consumables beyond the specially treated paper.
Key advantages of direct thermal printing include:
- Lower initial equipment costs
- No need for ink, toner, or ribbons
- Quieter operation compared to impact printers
- Ideal for high-volume, short-lifespan prints
Thermal transfer
Thermal transfer printing involves the use of a heat-sensitive ribbon containing ink. The printhead heats the ribbon, transferring the ink onto the printing medium. This method offers greater versatility in terms of print longevity and material compatibility, making it suitable for a wider range of applications.
Thermal transfer printing excels in scenarios requiring:
- Long-lasting, durable prints
- Printing on various materials, including synthetics
- Resistance to harsh environmental conditions
- High-quality barcodes and intricate graphics
Longevity and durability
While traditional thermal prints have limitations in terms of longevity, especially when exposed to heat or UV light, newer technologies like ZINK (Zero Ink) are pushing the boundaries of thermal printing durability. ZINK technology embeds color-forming molecules into the paper itself, activated by precise heat application, resulting in full-color prints without the need for ink cartridges.
ZINK prints offer superior fade resistance and durability compared to conventional thermal prints, making them suitable for long-term archival purposes.
Thermal printhead engineering: key components and innovations
The heart of any thermal printer is its printhead, a marvel of modern engineering that combines precision, durability, and efficiency. Understanding the key components and recent innovations in thermal printhead technology is crucial for appreciating the advancements in print quality and speed.
Thin film technology in modern thermal printheads
Modern thermal printheads utilize thin film technology to create heating elements that are both precise and energy-efficient. This technology allows for higher dot densities, resulting in sharper prints and the ability to reproduce finer details. The use of thin film also contributes to faster heating and cooling cycles, enabling higher print speeds without compromising quality.
Ceramic substrate integration for heat distribution
The ceramic substrate in thermal printheads plays a crucial role in heat distribution and management. High-quality ceramic materials ensure even heat distribution across the printhead, preventing hot spots that could lead to inconsistent print quality or premature wear. Advanced ceramic composites also contribute to the overall durability of the printhead, extending its operational lifespan.
Glaze layer optimization for print quality enhancement
The glaze layer on a thermal printhead serves as a protective barrier and plays a significant role in print quality. Recent innovations in glaze layer formulations have led to improvements in:
- Print contrast and density
- Resistance to abrasion and wear
- Thermal efficiency and energy consumption
These advancements collectively contribute to higher print quality, increased printhead longevity, and reduced maintenance requirements.
Maintenance-free operation: Self-Cleaning and Auto-Calibration features
One of the most significant advantages of thermal printers is their low maintenance requirements. Modern thermal printers incorporate self-cleaning mechanisms and auto-calibration features that significantly reduce the need for manual intervention.
Self-cleaning features typically involve automated routines that remove dust and debris from the printhead, ensuring consistent print quality over time. Auto-calibration systems adjust printing parameters based on environmental conditions and media characteristics, optimizing print quality and reducing waste.
The combination of self-cleaning and auto-calibration features in thermal printers can reduce maintenance downtime by up to 80% compared to traditional printing technologies.
Energy efficiency: thermal printing vs. inkjet and laser technologies
In an era where energy efficiency is paramount, thermal printing technology stands out for its low power consumption compared to inkjet and laser printing methods. This efficiency translates into lower operational costs and a reduced environmental footprint for businesses.
Power consumption metrics: watts per page analysis
A comparative analysis of power consumption reveals that thermal printers typically consume fewer watts per page printed than their inkjet or laser counterparts. This efficiency is particularly pronounced in high-volume printing scenarios, where the cumulative energy savings can be substantial.
Standby mode innovations: Instant-On capabilities
Thermal printers excel in their instant-on capabilities, requiring minimal warm-up time compared to laser printers. This feature not only contributes to energy savings but also enhances productivity by reducing wait times between print jobs.
Thermal management systems: heat dissipation techniques
Effective thermal management is crucial for maintaining energy efficiency and print quality. Modern thermal printers employ advanced heat dissipation techniques, including:
- Passive cooling systems utilizing heat sinks
- Active cooling with small, energy-efficient fans
- Smart power management algorithms
These thermal management systems ensure optimal performance while minimizing energy consumption, contributing to the overall efficiency of thermal printing solutions.