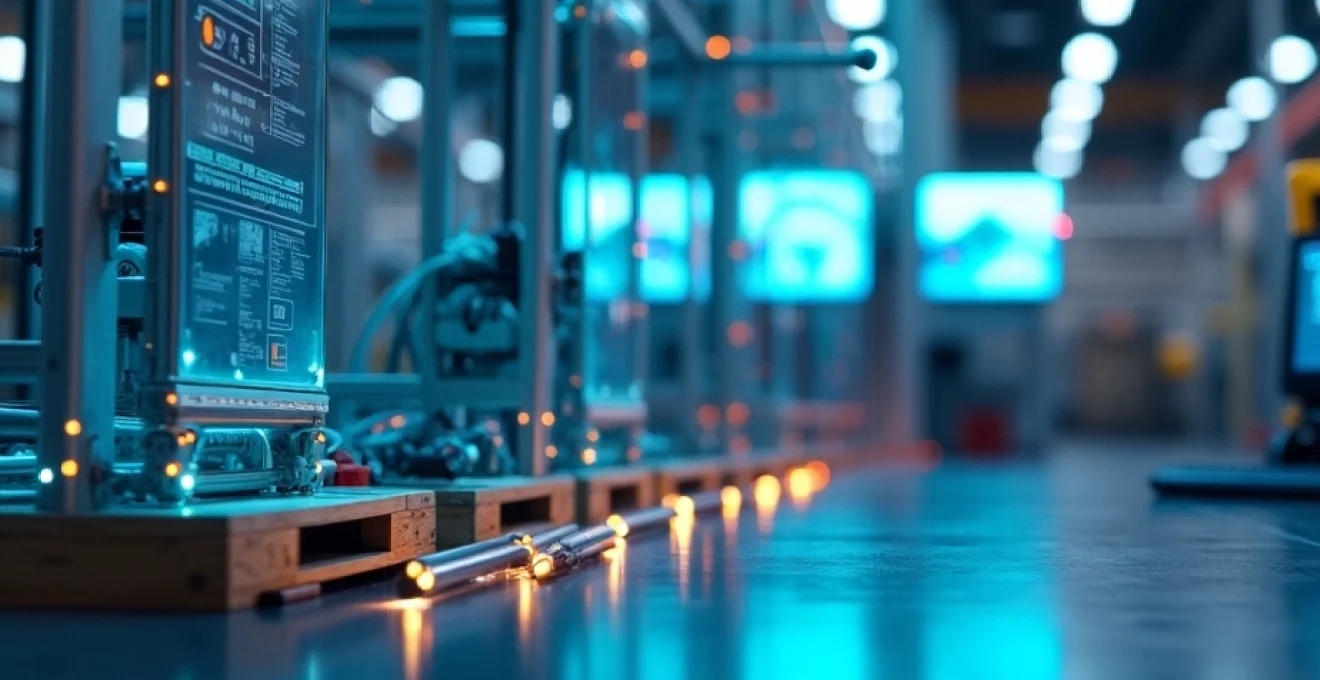
Automated systems have revolutionized industrial processes, transforming manufacturing landscapes and redefining efficiency standards. By leveraging cutting-edge technologies, these systems streamline operations, minimize human error, and optimize resource utilization. The integration of automation in industrial settings has become a cornerstone for companies aiming to maintain a competitive edge in today's fast-paced market. From enhancing product quality to reducing operational costs, automated systems are driving unprecedented levels of productivity and precision across various industrial sectors.
Integration of programmable logic controllers (PLCs) in manufacturing
Programmable Logic Controllers (PLCs) have emerged as the backbone of industrial automation, providing a robust and flexible foundation for controlling complex manufacturing processes. These sophisticated devices act as the central nervous system of automated production lines, coordinating various components and ensuring seamless operation. By utilizing PLCs, manufacturers can significantly reduce downtime, improve product consistency, and respond swiftly to changing production demands.
One of the key advantages of PLCs is their ability to process information in real-time, allowing for immediate adjustments to production parameters. This rapid response capability enables manufacturers to maintain optimal performance levels and address potential issues before they escalate. Moreover, PLCs offer scalability, allowing businesses to expand their automation infrastructure as their operations grow.
The integration of PLCs has also facilitated the implementation of advanced control algorithms, such as model predictive control and adaptive control systems . These sophisticated control strategies enable manufacturers to fine-tune their processes with unprecedented precision, resulting in improved product quality and reduced waste. Additionally, the modular nature of PLC systems allows for easy maintenance and upgrades, ensuring that manufacturing facilities can stay at the forefront of technological advancements.
Advanced robotics and cobot systems in assembly lines
The advent of advanced robotics and collaborative robots (cobots) has ushered in a new era of efficiency in assembly line operations. These intelligent machines work alongside human operators, combining the precision and tirelessness of automation with the flexibility and problem-solving skills of human workers. The result is a harmonious blend of man and machine that maximizes productivity while ensuring workplace safety.
Collaborative robots: FANUC CR series and universal robots UR10
Collaborative robots, such as the FANUC CR Series and Universal Robots UR10, have redefined the concept of human-robot interaction in industrial settings. These cobots are designed with advanced safety features that allow them to work in close proximity to humans without the need for protective barriers. The FANUC CR Series, for instance, incorporates sensitive force sensors that enable the robot to detect and respond to contact, ensuring safe operation even in dynamic environments.
The Universal Robots UR10, known for its versatility and ease of programming, has found applications in various industries, from automotive to electronics manufacturing. Its user-friendly interface allows for quick deployment and reprogramming, making it an ideal solution for companies with frequently changing production requirements. By automating repetitive tasks, these cobots not only improve efficiency but also reduce the risk of repetitive strain injuries among human workers.
Machine vision systems: Cognex In-Sight and KEYENCE CV-X series
Machine vision systems have become indispensable in quality control and inspection processes. The Cognex In-Sight and KEYENCE CV-X Series represent the cutting edge of this technology, offering high-speed, high-precision visual inspection capabilities. These systems can detect defects and inconsistencies that would be challenging or impossible for human inspectors to identify consistently.
The Cognex In-Sight vision systems are renowned for their robust pattern matching algorithms and ability to perform complex measurements in real-time. This technology enables manufacturers to implement 100% inspection protocols without sacrificing production speed. Similarly, the KEYENCE CV-X Series offers advanced image processing capabilities, allowing for multi-point inspections and 3D measurements with exceptional accuracy.
By integrating these machine vision systems into assembly lines, manufacturers can significantly reduce defect rates and improve overall product quality. The ability to capture and analyze vast amounts of visual data also provides valuable insights for process optimization and predictive maintenance.
End-of-Arm Tooling (EOAT) innovations: soft robotics mgrip
End-of-Arm Tooling (EOAT) plays a crucial role in the versatility and effectiveness of robotic systems. The Soft Robotics mGrip represents a paradigm shift in EOAT design, offering unparalleled flexibility in handling diverse objects. This innovative gripping system utilizes soft, compliant materials that can conform to various shapes and sizes, making it ideal for industries dealing with delicate or irregularly shaped products.
The mGrip's adaptive nature allows for rapid changeovers between different product lines without the need for complex reprogramming or tool changes. This flexibility translates to reduced downtime and increased overall equipment effectiveness (OEE). Furthermore, the gentle gripping action of the mGrip minimizes the risk of product damage, making it particularly valuable in industries such as food processing and packaging where product integrity is paramount.
Ai-driven path planning: ROS-Industrial framework
Artificial Intelligence (AI) has made significant inroads into robotic path planning, with the ROS-Industrial framework emerging as a powerful tool for optimizing robot movements. This open-source platform enables developers to implement advanced AI algorithms that can dynamically adjust robot trajectories based on real-time environmental data.
The ROS-Industrial framework facilitates the creation of more efficient and adaptable robotic systems. By leveraging machine learning techniques, robots can continuously improve their performance, learning from past operations to optimize future movements. This AI-driven approach results in smoother, more energy-efficient robot motions, reduced cycle times, and improved overall system reliability.
Moreover, the framework's compatibility with a wide range of industrial robots and sensors allows for seamless integration into existing automation infrastructures. This interoperability is crucial for businesses looking to upgrade their automation capabilities without overhauling their entire production setup.
Industrial Internet of Things (IIoT) for Real-Time monitoring
The Industrial Internet of Things (IIoT) has emerged as a game-changer in the realm of industrial automation, enabling unprecedented levels of connectivity and data-driven decision-making. By creating a network of interconnected devices and sensors, IIoT facilitates real-time monitoring of every aspect of the production process, from individual machine performance to overall system efficiency.
Sensor Networks: implementing MQTT protocol
At the heart of IIoT implementations lies the sensor network, which serves as the primary data collection mechanism. The MQTT (Message Queuing Telemetry Transport) protocol has become the de facto standard for IIoT communications due to its lightweight nature and efficient bandwidth utilization. This publish-subscribe messaging protocol allows for seamless data transfer between devices, even in environments with limited network resources.
Implementing MQTT in industrial settings enables real-time data streaming from a multitude of sensors, providing a comprehensive view of the production environment. This constant flow of information allows for immediate detection of anomalies and rapid response to potential issues, minimizing downtime and optimizing overall equipment effectiveness (OEE).
Edge computing with Siemens MindSphere
Edge computing has revolutionized the way industrial data is processed and analyzed. Platforms like Siemens MindSphere bring computing power closer to the data source, enabling real-time analysis and decision-making at the edge of the network. This approach significantly reduces latency and bandwidth requirements while enhancing data security and privacy.
Siemens MindSphere offers a robust suite of tools for edge computing, allowing manufacturers to process critical data on-site before transmitting aggregated insights to the cloud. This hybrid approach optimizes network performance and enables faster response times to production issues. Additionally, MindSphere's open architecture facilitates integration with existing systems, making it an ideal solution for businesses looking to gradually transition to a fully connected Industry 4.0 environment.
Predictive maintenance using IBM watson IoT platform
Predictive maintenance has emerged as one of the most impactful applications of IIoT technology, with platforms like IBM Watson IoT leading the charge. By leveraging advanced analytics and machine learning algorithms, Watson IoT can predict equipment failures before they occur, allowing maintenance teams to address issues proactively rather than reactively.
The IBM Watson IoT Platform aggregates data from various sources, including sensor readings, historical maintenance records, and environmental factors, to create comprehensive equipment health profiles. These profiles are continuously updated and analyzed to detect patterns indicative of impending failures. By accurately predicting maintenance needs, manufacturers can significantly reduce unplanned downtime, extend equipment lifespan, and optimize maintenance schedules.
Predictive maintenance powered by IIoT has been shown to reduce maintenance costs by up to 25% and unplanned outages by up to 50% in some industries.
Machine learning in quality control processes
Machine Learning (ML) has revolutionized quality control processes in industrial settings, offering unprecedented levels of accuracy and efficiency. By analyzing vast amounts of data from various sources, ML algorithms can identify subtle patterns and anomalies that would be impossible for human inspectors to detect consistently. This capability has led to significant improvements in defect detection rates and overall product quality.
One of the key advantages of ML in quality control is its ability to adapt and improve over time. As these systems process more data, they become increasingly adept at identifying defects and predicting potential quality issues. This continuous learning process ensures that quality control measures remain effective even as production processes evolve or new product variations are introduced.
Moreover, ML-powered quality control systems can operate tirelessly around the clock, maintaining consistent performance levels that human inspectors simply cannot match. This 24/7 vigilance ensures that every product undergoes the same rigorous inspection process, regardless of when it was manufactured.
Digital twin technology for process optimization
Digital Twin technology has emerged as a powerful tool for process optimization in industrial settings. By creating a virtual replica of physical assets and processes, manufacturers can simulate, analyze, and optimize their operations in a risk-free digital environment. This approach allows for extensive testing and refinement of production strategies without the need for costly physical prototypes or production line downtime.
Creating virtual models with autodesk Fusion 360
Autodesk Fusion 360 has become a go-to platform for creating comprehensive digital twins of industrial processes. Its cloud-based architecture and powerful modeling capabilities enable engineers to develop highly accurate virtual representations of entire production lines. These models incorporate not only the physical dimensions of equipment but also their operational characteristics and interdependencies.
By leveraging Fusion 360's simulation tools, manufacturers can perform detailed analyses of their production processes, identifying bottlenecks and inefficiencies that may not be apparent in the physical world. This insight allows for data-driven optimization of production layouts, machine settings, and workflow sequences, leading to significant improvements in overall efficiency and output quality.
Real-time simulation using ANSYS twin Builder
ANSYS Twin Builder takes digital twin technology a step further by enabling real-time simulation of industrial processes. This advanced platform integrates with live data streams from physical assets, creating a dynamic digital twin that evolves in tandem with its real-world counterpart. This real-time capability allows for immediate detection of performance deviations and rapid response to changing conditions.
The predictive analytics capabilities of ANSYS Twin Builder enable manufacturers to forecast equipment behavior and performance under various scenarios. This foresight is invaluable for optimizing maintenance schedules, predicting potential failures, and planning for future production demands. By simulating different operational strategies, companies can make informed decisions that maximize efficiency and minimize risks.
Integration with PLCs via OPC UA standard
The integration of digital twins with physical systems is facilitated by the OPC UA (Unified Architecture) standard, which provides a secure and reliable communication protocol between industrial devices and software applications. This integration allows for bidirectional data flow, enabling digital twins to not only receive real-time data from PLCs but also send optimized control parameters back to the physical systems.
By leveraging OPC UA, manufacturers can create a seamless connection between their virtual models and actual production environments. This tight integration ensures that digital twins remain accurate and up-to-date, providing a reliable basis for decision-making and process optimization. Furthermore, the standardized nature of OPC UA facilitates interoperability between different vendors' systems, allowing for more flexible and scalable automation solutions.
Automated guided vehicles (AGVs) in material handling
Automated Guided Vehicles (AGVs) have revolutionized material handling in industrial settings, offering unparalleled efficiency and flexibility in logistics operations. These autonomous vehicles navigate factory floors and warehouses, transporting materials, components, and finished products with precision and reliability. The implementation of AGV systems has led to significant improvements in operational efficiency, reduced labor costs, and enhanced workplace safety.
SLAM navigation: implementing velodyne LiDAR systems
At the core of modern AGV navigation systems is Simultaneous Localization and Mapping (SLAM) technology, which allows vehicles to create and update maps of their environment in real-time while simultaneously tracking their position within that environment. Velodyne LiDAR systems have emerged as a leading solution for implementing SLAM in industrial AGVs, offering high-resolution 3D mapping capabilities that enable precise navigation even in dynamic environments.
The integration of Velodyne LiDAR technology in AGVs provides several key advantages:
- Accurate obstacle detection and avoidance, even in complex or changing environments
- Enhanced ability to operate in low-light conditions or areas with varying lighting
- Improved efficiency in path planning, resulting in optimized travel routes and reduced congestion
- Increased safety through real-time environment monitoring and rapid response to unexpected obstacles
By leveraging these advanced LiDAR systems, AGVs can navigate with unprecedented accuracy and adaptability, significantly enhancing the overall efficiency of material handling operations.
Fleet management software: savant automation WMS integration
Effective management of AGV fleets is crucial for maximizing the benefits of automated material handling systems. Savant Automation's Warehouse Management System (WMS) integration offers a comprehensive solution for coordinating and optimizing AGV operations. This sophisticated software platform provides real-time visibility into AGV status, locations, and task assignments, enabling seamless coordination with other warehouse operations.
Key features of Savant Automation's WMS integration include:
- Dynamic task allocation based on real-time priorities and AGV availability
- Optimized route planning to minimize travel time and energy consumption
- Predictive maintenance scheduling to maximize AGV uptime
- Integration with inventory management systems for accurate stock tracking
- Detailed performance analytics for continuous process improvement
By leveraging these advanced fleet management capabilities, manufacturers can ensure that their AGV systems operate at peak efficiency, maximizing throughput and minimizing operational disruptions.
Safety systems: SICK microScan3 core safety laser scanners
Safety is paramount in AGV operations, and the SICK microScan3 Core Safety Laser Scanners represent the cutting edge in AGV safety technology. These advanced sensors provide a 360-degree safety field around AGVs, ensuring the detection of any obstacles or personnel in the vehicle's path. The high-resolution scanning capabilities of the microScan3 allow for precise safety zone configuration, optimizing the balance between operational efficiency and workplace safety.
The implementation of SICK microScan3 scanners offers several critical benefits:
- Customizable safety fields that can adapt to different operational contexts
- Rapid response times for immediate stopping or speed reduction when obstacles are detected
- Robust performance in challenging industrial environments, including those with dust or vibration
- Easy integration with AGV control systems for seamless safety management
By incorporating these advanced safety systems, manufacturers can ensure that their AGV operations comply with the highest safety standards while maintaining optimal productivity levels. The integration of such sophisticated safety measures not only protects workers but also enhances overall operational reliability by minimizing the risk of accidents and associated downtime.
The implementation of advanced AGV systems with integrated safety features has been shown to reduce material handling accidents by up to 70% in some manufacturing facilities, while simultaneously improving logistics efficiency by 30% or more.
As industrial processes continue to evolve, the role of automated systems in improving efficiency becomes increasingly crucial. From the integration of PLCs and advanced robotics to the implementation of IIoT and digital twin technologies, these innovations are reshaping the manufacturing landscape. By embracing these automated solutions, companies can
not only enhance their operational efficiency but also gain a competitive edge in an increasingly automated world. The integration of these technologies is not just about improving individual processes; it's about creating a holistic, interconnected manufacturing ecosystem that can adapt and evolve in real-time.