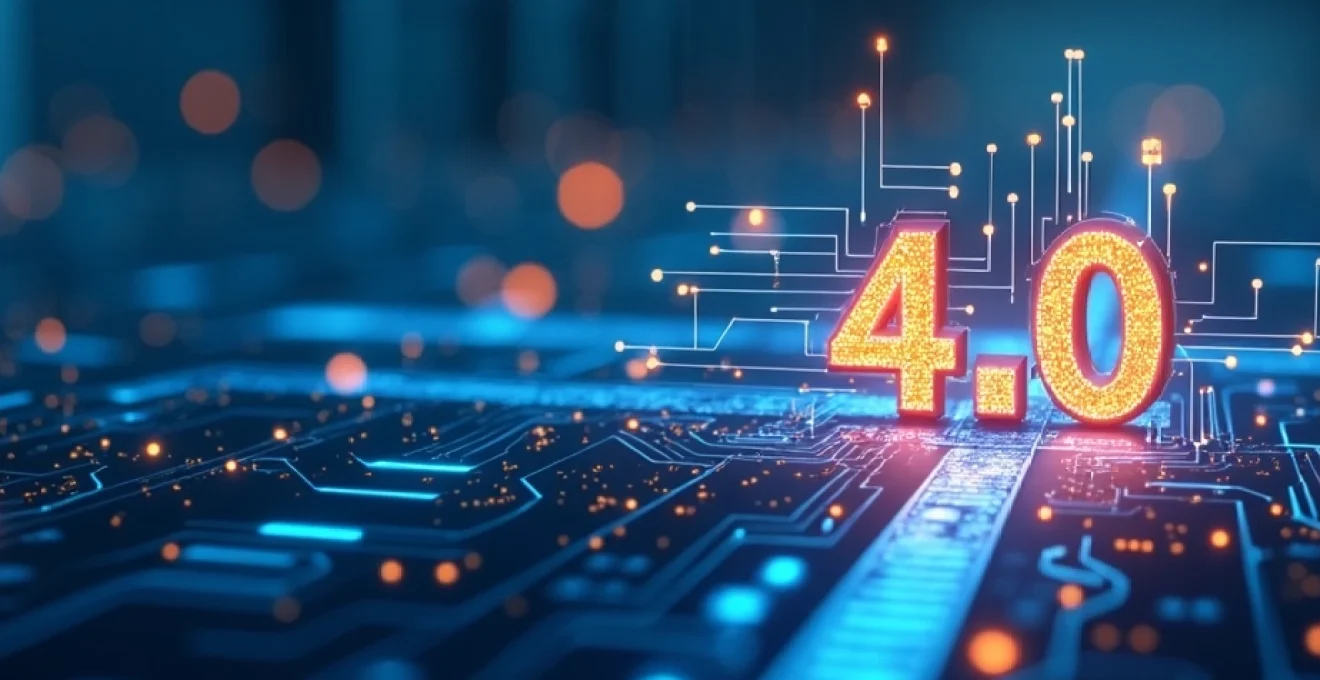
The manufacturing landscape is undergoing a profound transformation as we enter the era of Industry 4.0. To remain competitive, manufacturers must embrace intelligent production methods that leverage cutting-edge technologies. These advanced systems not only enhance efficiency and productivity but also enable unprecedented levels of customization and quality control. As the digital revolution reshapes industrial processes, companies that fail to adapt risk falling behind their more innovative counterparts.
Industry 4.0 technologies driving intelligent production
At the heart of intelligent production lies a suite of interconnected technologies that form the backbone of Industry 4.0. These technologies work in concert to create smart factories capable of self-optimization, self-configuration, and even self-diagnosis. The convergence of physical and digital systems is revolutionizing manufacturing processes, enabling real-time decision-making and unprecedented levels of efficiency.
Key technologies driving this transformation include the Internet of Things (IoT), artificial intelligence (AI), machine learning (ML), big data analytics, and cloud computing. These innovations allow for the creation of cyber-physical systems where machines communicate with each other and with human operators seamlessly. The result is a highly responsive and adaptive production environment that can quickly adjust to changing market demands and operational conditions.
One of the most significant advantages of Industry 4.0 technologies is their ability to generate and analyze vast amounts of data. This data-driven approach enables manufacturers to gain deep insights into their operations, identify inefficiencies, and make informed decisions to optimize production processes. By leveraging these technologies, companies can achieve higher levels of productivity, reduce waste, and improve overall equipment effectiveness (OEE).
Implementing AI-Powered predictive maintenance systems
One of the most impactful applications of intelligent production methods is the implementation of AI-powered predictive maintenance systems. These advanced systems leverage machine learning algorithms and real-time data analysis to predict equipment failures before they occur, dramatically reducing unplanned downtime and maintenance costs. By shifting from reactive to proactive maintenance strategies, manufacturers can optimize their operations and extend the lifespan of their assets.
Machine learning algorithms for fault detection
At the core of predictive maintenance systems are sophisticated machine learning algorithms designed to detect patterns and anomalies in equipment behavior. These algorithms analyze historical and real-time data from various sources, including sensors, maintenance records, and operational logs. By identifying subtle changes in machine performance, these systems can predict potential failures with remarkable accuracy, allowing maintenance teams to address issues before they escalate into costly breakdowns.
Iot sensors and Real-Time data collection
The effectiveness of predictive maintenance relies heavily on the continuous collection of high-quality data. IoT sensors play a crucial role in this process, providing a constant stream of real-time information about equipment performance, environmental conditions, and operational parameters. These sensors can monitor various aspects of machine health, including vibration, temperature, pressure, and energy consumption. The data collected by these sensors serves as the foundation for AI-driven analysis and decision-making.
Predictive analytics tools: IBM Maximo, GE Predix
To harness the full potential of predictive maintenance, manufacturers are turning to advanced analytics platforms specifically designed for industrial applications. Two prominent examples are IBM Maximo and GE Predix. These powerful tools integrate AI and machine learning capabilities with robust data management and visualization features, enabling manufacturers to gain actionable insights from their maintenance data. By leveraging these platforms, companies can optimize their maintenance schedules, reduce spare parts inventory, and minimize the risk of unexpected equipment failures.
Digital twin technology for equipment monitoring
Digital twin technology is emerging as a game-changer in predictive maintenance. A digital twin is a virtual replica of a physical asset or system that accurately simulates its behavior and performance. By creating digital twins of critical equipment, manufacturers can monitor and analyze their assets in real-time, perform virtual simulations, and predict future performance under various conditions. This technology enables maintenance teams to identify potential issues early, optimize equipment settings, and even test different maintenance strategies without affecting actual production.
Advanced robotics and collaborative automation
The integration of advanced robotics and collaborative automation is revolutionizing manufacturing floors across industries. These technologies are not only enhancing productivity and precision but also creating safer and more flexible work environments. As robots become more sophisticated and capable of working alongside humans, manufacturers are discovering new ways to optimize their production processes and adapt to changing market demands.
Autonomous Mobile Robots (AMRs) in manufacturing
Autonomous Mobile Robots (AMRs) are transforming material handling and logistics within manufacturing facilities. Unlike traditional automated guided vehicles (AGVs), AMRs use advanced sensors and AI to navigate dynamically through complex environments. These robots can efficiently transport materials, components, and finished products across the factory floor, optimizing workflow and reducing human labor requirements for non-value-added tasks. AMRs are particularly valuable in facilities with frequently changing layouts or those requiring flexible material transport solutions.
Cobots: integration with human workforce
Collaborative robots, or cobots, represent a significant advancement in human-robot interaction on the factory floor. These robots are designed to work safely alongside human operators, combining the strength, precision, and consistency of automation with the flexibility and problem-solving skills of human workers. Cobots are particularly useful for tasks that require a delicate balance of automation and human intervention, such as assembly processes or quality inspections. By seamlessly integrating cobots into their workforce, manufacturers can achieve higher levels of productivity while enhancing worker safety and job satisfaction.
Computer vision systems for quality control
Computer vision systems are revolutionizing quality control processes in manufacturing. These AI-powered visual inspection systems can detect defects and inconsistencies with a level of accuracy and speed that far surpasses human capabilities. By leveraging deep learning algorithms and high-resolution cameras, computer vision systems can identify even the most subtle flaws in products or components. This technology not only improves overall product quality but also reduces the need for manual inspections, allowing human workers to focus on more complex and value-added tasks.
RPA (Robotic Process Automation) in production planning
Robotic Process Automation (RPA) is extending the benefits of automation beyond the physical realm of manufacturing into administrative and planning processes. RPA tools can automate repetitive, rule-based tasks such as data entry, inventory management, and order processing. In production planning, RPA can significantly enhance efficiency by automating the creation of production schedules, managing material requirements, and generating reports. By reducing manual data handling and streamlining administrative processes, RPA frees up valuable human resources for more strategic decision-making and problem-solving activities.
Data-driven decision making with manufacturing execution systems (MES)
In the era of intelligent production, data-driven decision making is paramount. Manufacturing Execution Systems (MES) serve as the central nervous system of smart factories, collecting, processing, and analyzing data from various sources across the production environment. These sophisticated systems provide real-time visibility into manufacturing operations, enabling managers to make informed decisions quickly and effectively.
MES platforms integrate with other enterprise systems, such as ERP (Enterprise Resource Planning) and PLM (Product Lifecycle Management) software, to create a comprehensive view of the entire manufacturing process. By consolidating data from multiple sources, MES provides valuable insights into production performance, quality metrics, resource utilization, and compliance adherence. This holistic approach to data management enables manufacturers to identify bottlenecks, optimize resource allocation, and continuously improve their processes.
One of the key benefits of MES is its ability to provide real-time production monitoring and control. Operators and managers can access up-to-the-minute information on production status, machine performance, and quality metrics through intuitive dashboards and reports. This real-time visibility allows for rapid response to production issues, minimizing downtime and reducing the risk of quality problems. Additionally, MES can automate data collection and reporting processes, reducing the potential for human error and ensuring data accuracy.
Leveraging digital thread for End-to-End product lifecycle management
The concept of the digital thread is revolutionizing how manufacturers approach product lifecycle management. A digital thread creates a seamless flow of data across the entire product lifecycle, from initial design and engineering through manufacturing, delivery, and even post-sale service. This continuous data stream enables unprecedented levels of collaboration, traceability, and optimization throughout the product's life.
PLM software integration: Siemens Teamcenter, Dassault ENOVIA
To fully leverage the digital thread concept, manufacturers are turning to advanced Product Lifecycle Management (PLM) software solutions. Platforms like Siemens Teamcenter and Dassault ENOVIA provide comprehensive suites of tools for managing product data, processes, and decisions throughout the entire lifecycle. These systems integrate seamlessly with CAD/CAM tools, manufacturing execution systems, and enterprise resource planning software to create a unified digital ecosystem.
By centralizing product data and making it accessible across different departments and stages of the lifecycle, PLM software enables better collaboration, faster decision-making, and more efficient product development processes. Engineers can easily track design changes, manufacturing teams can access up-to-date product specifications, and service technicians can reference accurate product information for maintenance and repairs.
Blockchain for supply chain traceability
Blockchain technology is emerging as a powerful tool for enhancing supply chain traceability and transparency in manufacturing. By creating an immutable, decentralized ledger of transactions and events, blockchain enables manufacturers to track materials, components, and finished products with unprecedented accuracy and security. This level of traceability is particularly valuable in industries with strict regulatory requirements or those dealing with high-value or sensitive products.
Implementing blockchain in the supply chain can help manufacturers combat counterfeiting, ensure compliance with regulations, and quickly trace the source of quality issues. Moreover, blockchain can facilitate more efficient and secure transactions between supply chain partners, reducing administrative overhead and improving trust among stakeholders.
Api-first approach for seamless system integration
To fully realize the benefits of the digital thread, manufacturers must ensure seamless integration between various systems and platforms. An API-first approach to software development and integration is becoming increasingly important in this context. By prioritizing the development of robust, well-documented APIs, manufacturers can create flexible, interoperable systems that can easily exchange data and functionality.
This approach enables manufacturers to build modular, scalable technology stacks that can adapt to changing business needs and technological advancements. It also facilitates easier integration with third-party systems and services, allowing manufacturers to leverage best-of-breed solutions across their operations without being locked into a single vendor ecosystem.
Additive manufacturing and 3D printing for rapid prototyping
Additive manufacturing, commonly known as 3D printing, is revolutionizing the product development process by enabling rapid prototyping and small-batch production. This technology allows manufacturers to create complex geometries and custom parts with unprecedented speed and flexibility, significantly reducing the time and cost associated with traditional prototyping methods.
The ability to quickly produce functional prototypes allows engineers to iterate designs more rapidly, test multiple concepts simultaneously, and gather valuable feedback early in the development process. This accelerated development cycle can lead to better product designs, faster time-to-market, and reduced overall development costs.
Moreover, additive manufacturing is increasingly being used for production applications, particularly for low-volume, high-value parts or customized products. Industries such as aerospace, medical devices, and automotive are leveraging 3D printing to produce complex components that would be difficult or impossible to manufacture using traditional methods. This capability is opening up new possibilities for product design and customization, allowing manufacturers to offer highly personalized products to their customers.
As additive manufacturing technologies continue to advance, we're seeing improvements in print speed, material properties, and surface finish quality. These advancements are expanding the range of applications for 3D printing in manufacturing, from tooling and fixtures to end-use parts and even large-scale structures. The integration of additive manufacturing into intelligent production systems is enabling new levels of flexibility and efficiency in manufacturing operations.
By adopting these intelligent production methods, manufacturers can position themselves at the forefront of the digital revolution in manufacturing. The integration of AI, IoT, advanced robotics, and data-driven decision-making tools creates a powerful ecosystem that drives efficiency, quality, and innovation. As the manufacturing landscape continues to evolve, those who embrace these technologies will be best equipped to meet the challenges and opportunities of the future, ensuring their competitiveness in an increasingly digital world.